

but I will say that I have tried it and for a non-professional like myself I could not notice a difference so take that for what its worth.
#RECIPE FOR HIGH HEAT CASTING PLASTER FIR GLASS PROFESSIONAL#
I know you can buy professional investment pre-made on the internet and probably get better results than I do with this home-brew version. In this step I will show you my method to mix the investment, this is a simple method for a typical home workshop without a vacuum pump or any fancy dedicated investment casting equipment. The location and size of these components is a science in itself, but as a general rule of thumb use a nice large sprue to aid with pouring and metal shrinking, and use alot of vents. If your part to cast is small enough, about grape size, vents may not be necessary as your sprue will provide enough room for the air to escape as your pouring. I prefer to glue them on later just in case I decide to add or subtract the amount of vents used. Vents can either be designed into the part, or printed after the fact and glued with hot melt glue.
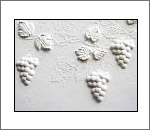
The vents will allow the metal to flow into areas that would otherwise be taken up by air that cannot escape, these vents also will allow metal to be pulled into thicker sections of the part as the molten aluminum is solidifying and shrinking. If there is a long flat section on your part then put a vent every couple of inches. the sprue is the large pyramid shaped piece you see in the picures which is where you will pour the molten metal. From my experience it is hard to put too many vents on your part, I will put a vent on every high point and larger sized vents at the end opposite of the sprue. I learned the hard way that these plastic parts have a lot of buoyancy in plaster investment so it is nice to have them held securely.

I also printed out the sprue and vents which also help with securing the part in the tub of investment. You can also print with as little infill as your comfortable with since these parts are not going to take any load and it will melt out faster with less material. These values change depending on many factors but 2-3% shrinkage for aluminum is a safe range to start with. I plan to drill out all the holes since they have to be a precise fit anyway. 040" or 1mm undersized at a minimum which allowed for shrinkage and imperfections. If you need a part to be accurate then you will have to account for extra shrinkage of the material you are casting with, in my case this is aluminum so I scaled the part about 2% larger and since the metal is shrinking the holes will actually get larger while the part gets smaller, all the holes about. Start out by printing your parts like you normally would. Orbital sander or some type of tool that makes strong vibrations.Cupcake pan or some sort of ingot mold to pour extra molten metal into.A way to melt your preferred metal, I used my homemade foundry furnace fired by a $40 propane burner I purchased from ebay.Good sized container with any type of sand, this is for mold support and safety in case the molten aluminum spills.3 buckets with flat bottoms for better mixing, 1 bucket to mix solids, 1 bucket with pre-measured water for the actual mixing, and 1 bucket with water for clean up.Tub of Plaster of Paris from art store "about $15".Bag of silica sand from a local material supplier "$6".PLA, ABS, or much preferred wax based filament like Moldlay filament "price varies".Well as I have proved here it does not have to be a expensive investment to get good results! I quickly realized the opportunities of this process could be endless so I thought I would share it with the rest of you. Traditionally known as investment casting this process has been a black art to some people and viewed as something not feasible to your standard DIY person due to the extravagant tools needed.
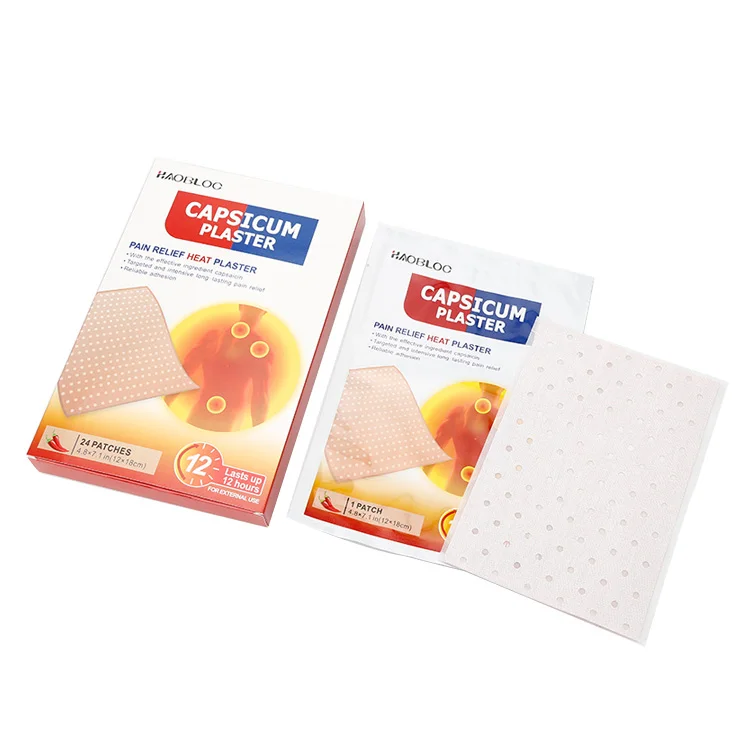
It was out of my price range to have it CNC machined so I took matters into my hands and came up with this. I learned this practice when I needed to make a custom shifter for my race car and a 3d printed plastic one just would not hold up to stress. Hi everyone I am going to share with you my method of turning a 3d printed part directly into a aluminum casting.
